As a field supervisor, it isn’t enough just to teach your crew about safety protocols. You also have to instill in them a conviction that those safety protocols are a top priority.
Otherwise, your team will view some safety tasks as a burden instead of a necessity. And they’ll skip over the safety rules that make tasks take longer. When that happens, there are often disastrous consequences.
To illustrate this better, here’s a tale of two hunters:
Two deer hunters went on a hunting trip. Both were avid sportsmen and had spent their entire lives hunting and fishing.
The first of these men had a safety-first mindset. He always brought a first-aid kit with him into the woods.
The second thought this was a tedious habit. He knew how to handle a gun and knife. So why take up space in his pack and add unnecessary weight? He had a task-first/safety second mindset.
But later that day the second hunter realized his folly. As he was using his knife, the blade slipped and slashed an artery in his hand. He was miles from civilization and in real trouble.
The first hunter saw what happened and ran to his pack. He grabbed a bottle of clotting powder from his safety-kit and poured it into his friend’s wound. The bleeding stopped.
The first hunter’s conviction that safety is the highest priority saved his friend’s life.
In the same way, if you and your crew have a deep-seated conviction that construction safety compliance comes first — even, before getting a job done quickly — then you can avoid the high costs that come with low safety standards.
The High Costs of Low Safety Standards
When it comes to jobsite safety, complacency is not an option. Choosing to do a job quickly instead of safely is never the right decision.
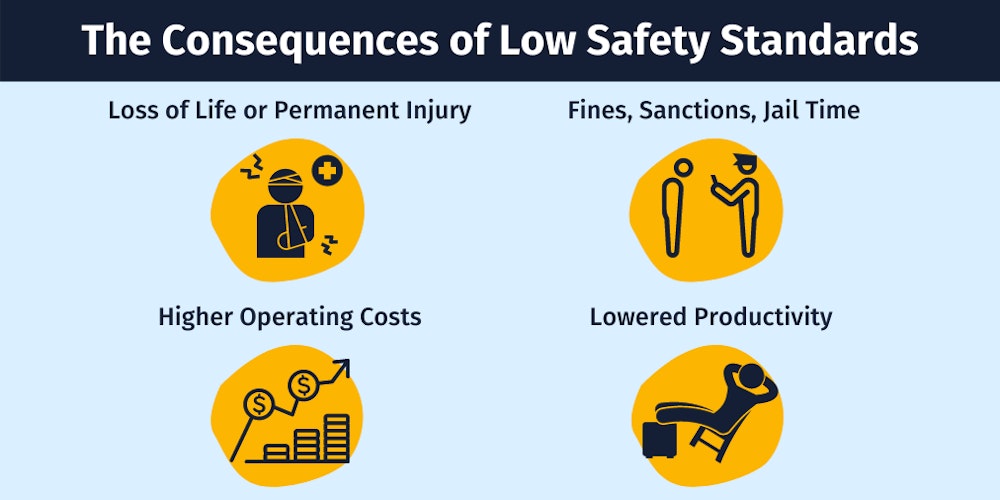
Here are just a few of the consequences that can come with lax safety measures:
Loss of Life or Permanent Injury
Safety compliance is a matter of life and death. In fact, the U.S. Bureau of Labor Statistics reports that every 99 minutes, someone dies because of a work-related accident.
Four of the top causes of death are falls, electrocutions, getting struck by objects, and getting caught by, or in-between, machinery, commonly known as the Fatal Four.
And sadly, these top causes of death coincide with OSHA’s top safety citations. In 2019, OSHA cited 6,010 fall protection violations, 2,606 lockout/tagout violations, 3,671 hazard communications violations, and 1,743 machine-guarding violations.
According to OSHA, “Eliminating the Fatal Four would save 591 workers’ lives in America every year.”
Fines, Sanctions, Jail Time
Loss of life and permanent injuries are the worst outcomes for ignoring safety compliance issues. But there’s another outcome that supervisors need to remember.
There’s a big difference between an unavoidable accident and one that could have been prevented if safety protocols were followed. The latter points toward negligence. And if the negligence lies with personnel supervisors, they will face serious repercussions.
Foremen, superintendents and supervisors who are at fault in a crew member's injury or death will not only have to live with guilt. They will also have to pay for their actions. At the very least, they will be fined for their negligence. At most, they will spend time in prison.
Whatever the consequence, it will cost much more than taking the time to consistently follow safety protocols in the first place.
Higher Operating Costs
Accidents also make job costs jump dramatically.
Here are the added costs that could result from a worksite accident:
- The cost of the injured worker’s salary while they are off the job and recovering
- The cost of an additional worker to replace them
- The repair costs of any damaged equipment and materials
- Contractual penalties that result because of delays caused by the accident
- Raised insurance costs
Lowered Productivity
Injured workers, damaged equipment, and investigations into accidents add up to lost time. And lost time means lost productivity.
This is a great thing to remember when you’re tempted to skip safety steps in order to save time. It only takes one bad accident to set your schedule back for weeks or even months.
You already know how costly a lack of safety compliance is. Here are some practical ways to help your workers adopt a safety-first mindset.
How to Help Your Crew Learn to Value Safety Compliance
In order for your crew to internalize the importance of safety, it has to be ingrained into your company’s culture. There should be an understanding that safety is always the right choice. And workers should value it enough to hold themselves and each other accountable.
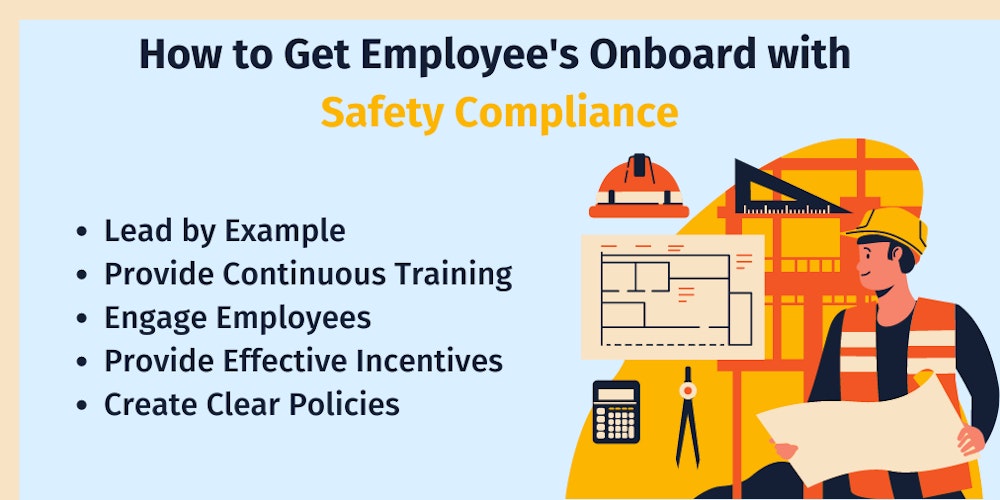
But that kind of culture doesn’t happen by accident. You have to be proactive if you want workers to get onboard. Here’s how:
Lead by Example
Before you can expect your team to adopt a safety-first mindset, you have to have one yourself. And you have to exemplify the kind of behaviors you want from your crew.
Attend every safety meeting. Keep quiet when you want to complain about a protocol that slows the work process. Always use your PPE.
Don’t be the excuse someone uses to make a bad safety decision.
Provide Continuous Training
Studies show that 70 percent of what’s covered in one-time training is forgotten within a day.
So hosting an occasional safety seminar is not enough. Safety training should be continuous. Schedule safety meetings every morning to keep safety top of mind.
Training should also be taken out of a classroom setting and modeled on the job. The best way to learn is by doing.
Engage Employees
If you want employees to buy into a safety-first mindset, involve them in the process.
Get workers’ input when selecting PPE and listen to them when they have an opinion. They might be quicker to see which kinds of protective equipment is better suited for their workflow. And if they are invested in selecting safety equipment, then they are more likely to use it.
Provide Effective Incentives
Using incentives and disciplinary consequences to hold crews accountable for their safety practices is helpful. But you have to be careful not to use either method in excess.
Punishment-based accountability models can shut down communication between employees and their supervisors. And employees can become fearful to admit when they’ve had an accident.
In fact, more than 25 percent of U.S. construction workers admit to suffering a worksite accident without reporting it. And the biggest reasons for keeping quiet were fear of punishment or losing out on a safety bonus.
Crew members should never feel afraid to ask any questions they have about safety procedures or become hesitant to report hazards. One way to ease the fears that come along with reporting safety violations is to incorporate technology or policies that allow workers to file reports anonymously.
Create Clear Policies
Unclear and inconsistent safety protocols will slow the adoption of a safety-first culture. Your employees can’t follow rules they don’t understand. And they will resist any safety protocol that isn’t enforced regularly.
Creating clear, consistent rules will reduce your crew’s resistance to following safety procedures.
Conclusion
A work culture that focuses on safety reduces accidents and saves lives. In fact, a report from Health and Safety at Work shows that construction firms in Hong Kong that introduced a culture of safety reduced workplace accidents by 75 percent.
So, the time and effort it takes to create a safety-first workforce is worth it.
If you’re a supervisor in the construction industry and you’re interested in more tips to succeed, check out this post: Construction Project Checklist to Help You Succeed.